Jump To:
How Hydrogen Gas Filters Enable a Renewable Future | Vantech
Hydrogen is driving innovation in clean energy. As a zero-emissions fuel, it offers a powerful, portable alternative to traditional lithium batteries, with superior energy storage potential. While hydrogen fuel infrastructure still lags behind fossil fuels, Vantech is actively advancing this technology by engineering high-performance, cost-effective Hydrogen Gas Filters to meet the increasing demands of this burgeoning industry.
Hydrogen fuel must be chilled, pressurized, and purified to protect sensitive fuel cell components and maintain system efficiency. Vantech’s Hydrogen Gas Filters meet these demands by removing contaminants such as water, oil, and particulates. Our range of filtration solutions – like our porous, non-woven sintered metal mesh filters, or our mission-critical woven mesh filters – ensure optimal hydrogen purity for applications ranging from fuel cell vehicles and dispensing stations to PEM Electrolysis systems, and everything in between.
Vantech’s hydrogen gas filters play a critical role in making hydrogen energy safer, more reliable, and commercially viable. Contact us today to learn how we can support your next hydrogen project!
Hydrogen Fuel Cell Filters come in a variety of forms to suit different applications, with sintered mesh filters commonly used to prevent particulates from entering and damaging the anode side of the Fuel Cell Stack. We custom-manufacture each filter to match specific operating conditions and technical requirements. These filters can withstand the pressure changes that occur when compressed hydrogen is depressurized for electrochemical reactions, and Vantech’s Hydrogen Gas Filters are engineered with these demands in mind.
During PEM Electrolysis, filtration downstream of the Electrolyser Stack protects coolers, purifiers, and compressors from damage. Particulates often result from membrane or catalyst degradation, water vapor, or microdroplets left behind after electrolysis. Our wide range of filters safeguard these components, supporting system longevity and reliability.
We custom-manufacture each filter to match specific operating conditions and technical requirements. One common example is the sintered mesh filter, which prevents particulate intrusion on the anode side of a PEM Fuel Cell Stack. These filters can withstand the pressure changes that occur when compressed hydrogen is depressurized for electrochemical reactions, and Vantech’s Hydrogen Gas Filters are engineered with these demands in mind.
Below are answers to some of the most commonly asked questions we receive about our Hydrogen Filters:
Frequently Asked Questions – FAQ
Why Are Hydrogen Fuel Cell Filters Important?
Hydrogen used in Fuel Cell Vehicles (FCVs) must meet ISO 14687 standards, which define very strict purity levels:
H2 Fuel Index (minimum mole fraction) | 99.7% |
Total non-hydrogen gases (maximum) | <300 µmol/mol |
Water | <5 µmol/mol |
Total Hydrocarbons except Methane | <2 µmol/mol |
Methane (CH4) | <100 µmol/mol |
Oxygen (O2) | <5µmol/mol |
Helium (He)/Nitrogen(N2)/Argon(Ar) | <300 µmol/mol |
Carbon Dioxide (CO2) | <2 µmol/mol |
Carbon Monoxide (CO) | <0.2 µmol/mol |
Total Sulphur (sulphur particle sizes range from 1-20 µm; aggregate from 5-20 µm) | <4ppb |
Maximum Particulate Concentration | 1 mg/kg in concentration |
Vantech’s Sintered Mesh Filters can remove particulates as small as 1 µm, effectively capturing contaminants that would compromise hydrogen purity. Even in closed hydrogen systems, particulates may accumulate during preparation stages. These may include metal shavings from compressor components, flakes from piping and welds (e.g., rust or weld slag), or contaminants such as dirt or oil introduced during maintenance. Filters are therefore essential to protect critical system components.
How Are Filters Used in Hydrogen Refueling Stations?
Hydrogen fueling stations include multiple systems to ensure the safe and efficient delivery of hydrogen to FCVs. As discussed, filtration is vital to ensure compliance with international standards. In stations with on-site H₂ generation, filters are required for the following reasons:
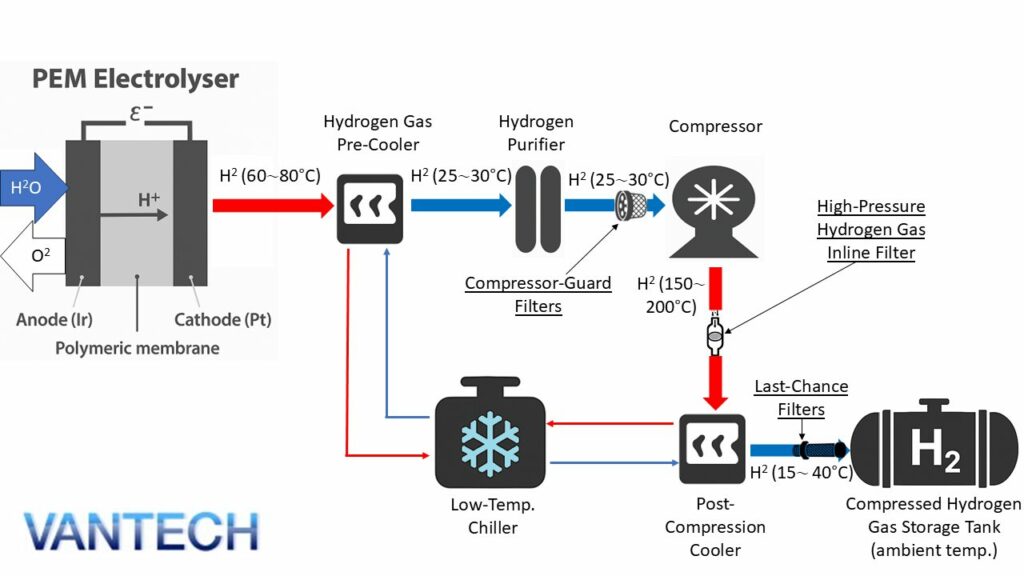
- Compressor Guard Filters: Downstream of the hydrogen purifiers to protect the compressor
- Hydrogen Gas Inline Filters: After the compressor to capture metal particles produced from wear and tear
- Last-Chance Filtens Upstream of the high-pressure hydrogen storage tank to ensure hydrogen purity
Even stations that don’t generate hydrogen on-site must still use hydrogen storage tanks and low-temperature chillers, both of which require particulate filters to remove contaminants present in piping or storage vessels. Filters can utilized in the following areas:
- Upstream and downstream of the ball-valve to capture lingering metal particulates such as rust of metal flakes
- Within the fuel dispenser (last-chance filtration before FCV entry)
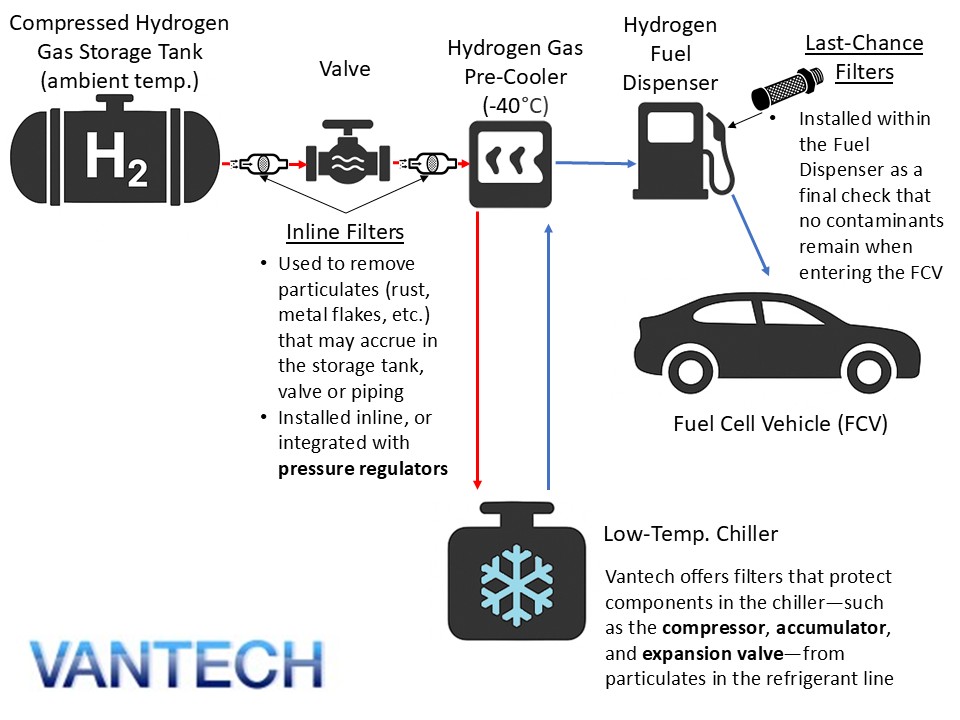
What Are the Challenges of Filtering High-Pressure Hydrogen?
Vantech’s hydrogen regulator filters are purpose-built to remove particulates from high-pressure hydrogen gas. The sintered metal filter media we use is engineered to withstand the extreme demands of hydrogen fuel cell systems—including the low temperatures used during fueling (–40 °C) and the high-pressure environments involved in hydrogen storage and regulation. These filters play a critical role in protecting system integrity as hydrogen is depressurized prior to entering the fuel cell stack, where lower pressure is required to prevent damage and ensure efficient PEM fuel cell operation. Vantech’s durable sintered metal filters offer solutions for high-pressure hydrogen filtration, ensuring that pressure changes do not compromise filtration performance.
What Uses Do Hydrogen Fuel Cells Offer?
Beyond their clean emissions, hydrogen fuel cells offer on-demand electricity generation and significantly higher energy density than lithium batteries, enabling longer vehicle ranges—especially in aviation drones and other high-endurance applications. While hydrogen infrastructure is still expanding, on-site hydrogen generation at refueling stations offers a unique advantage over gasoline. FCVs refuel in just 3–10 minutes when connected to a hydrogen gas dispenser, compared to up to an hour for EVs. Additionally, with limited global lithium supplies, hydrogen fuel cells—requiring only small amounts of platinum—present a scalable alternative for the decarbonization of transportation.
Why Must Hydrogen Gas Be Cooled Before Use?
When the hydrogen gas from a refueling station enters the FCV via the fuel dispenser, it must be cooled to –40 °C to prevent excessive heat buildup in the vehicle’s storage tank. H₂ gas produced by the Electrolyser Stack during PEM Electrolysis must also be compressed for storage—typically to 350–700 bar (and up to ~875 bar in some systems). However, compressing gas naturally increases its temperature (sometimes above 150 °C/302 °F), so the gas must be chilled before storage to reduce thermal stress on components and to maximize storage density. Vantech manufactures both sintered and woven mesh filters for use in compressor and chiller systems, offering a range of materials and specifications for specialized applications. For more information on our extensive range of hydrogen fuel related metal filters and strainers, select an option below or contact us for a custom-manufactured solution!